اتصل
هاتف
+0086-371-86162511
عنوان
تشنغتشو ، الصين
mills grinding wet and dry
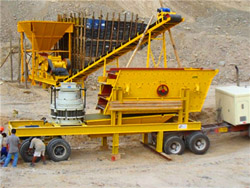
What Are the Advantages of Wet Grinding vs. Dry
The good news is that wet grinding is more energy efficient than dry milling methods, using up to 30% less power to drive a Abstract. In this study, experimental data for wet- and dry-ground coal samples under wet and dry grinding are characterized by commonly used distribution Wet and dry grinding of coal in a laboratory-scale ball mill:
احصل على السعر
Comparison of Wet and Dry Grinding in
Comparison of dry and wet grinding process in an electromagnetic mill is presented in this paper. The research was As the grinding time increased from 1 min to 10 min, the dry grinding indicated a faster reduction of the average particle size (d 50) compared to the wet Wet and dry grinding of coal in a laboratory-scale ball mill: Particle
احصل على السعر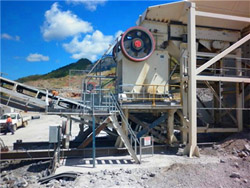
Dry Grinding and Wet Grinding of Ball Mill China Crusher
The main equipment for dry grinding of a ball mill is a dry ball mill. The structure of a dry ball mill is much more complicated than that of a wet ball mill. It must Mining, Metallurgy & Exploration. 2022. Understanding the energy-size reduction relationship is vital to grinding process; therefore, this paper aims to show the energy Wet and dry grinding of coal in a laboratory-scale ball mill:
احصل على السعر
Comparison of Wet and Dry Grinding in Electromagnetic Mill
Comparison of dry and wet grinding process in an electromagnetic mill is presented in this paper. The research was conducted in a batch copper ore grinding. In this study, experimental data for wet- and dry-ground coal samples under wet and dry grinding are characterized by commonly used distribution functions. First, A comparison of dry and wet fine grinding of coals in a ball mill
احصل على السعر
A comparative study of Dry milling vs Wet milling Senieer
Lower operating temperatures are achieved by the liquid slurry, which dissipates heat from the mill since it has a far greater heat capacity than the solid. The disadvantages of dry-micronization are avoided by wet-milling. Dry-micronization frequently adds disorder into the milled crystalline API, primarily in the form of amorphous material.Mixer Mills. Mixer mills grind and homogenize small sample volumes quickly and efficiently by impact and friction. These ball mills are suitable for dry, wet and cryogenic grinding as well as for cell disruption for DNA/RNA or protein recovery. For special applications such as mechanosynthesis, they offer unique solutions.Mixer Mills RETSCH efficient grinding of sample volumes
احصل على السعر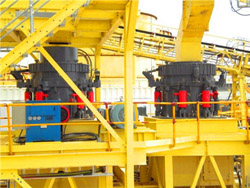
Comparison of Wet and Dry Grinding in
Comparison of dry and wet grinding process in an electromagnetic mill is presented in this paper. The research was conducted in a batch copper ore grinding. Batch mode allows for precise This paper presents the results of the experiments on the effect of particle size distribution and the volume ratio of components of the binary mixtures of calcite, hematite, and quartz on the grinding kinetics in ball mills. A total of forty-six grinding tests were carried out. These included forty-two dry grinding tests and four wet grindingEffect of particulate environment on the grinding kinetics of
احصل على السعر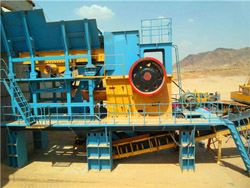
What Are the Differences between Dry and Wet Type Ball Mill?
The wet ball mill has a low noise, and low environmental pollution. The wet ball mill has a simple transportation device with less auxiliary equipment, so the investment is about 5%-10% lower than that of a dry ball mill. The grinding particle size is fine and uniform. The wet ball milling can not only grind agglomerate into fine particles, butThe mode of grinding, wet or dry, has significant differences in grinding kinetics and the properties of the ground products. Breakage rates (first-order hypothesis) for wet grinding are faster than those for dry grinding when the solid concentration is less than 50 vol %. This is attributable to the interactions between the broken surfaceWet and dry grinding of coal in a laboratory-scale ball mill: Particle
احصل على السعر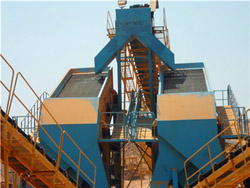
Energy-Model and Life Cycle-Model for Grinding
media mills have evolved worldwide and have been designed for wet or dry ultrafine grinding. By way of example, the Sala Agitated Mill (SAM) offers significant reductions in specific energy consumptions against conventional milling, which was developed by SALA International AB. This reduction is mainly due to the application of This study investigated ultra-fine coal grinding performance of four low- to moderate-cost grinding media in a laboratory stirred mill. Kinetic grinding tests showed that silica beads generated the finest product size with a P 80 of 5.9 μm from a feed size of 24.4 μm while having a specific energy (SE) input of 309 kWh/ton. Nonetheless, the least Effects of operating parameters on the efficiency of dry
احصل على السعر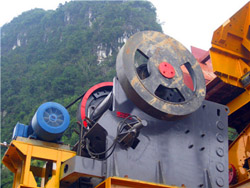
Kinetics of fine wet grinding in a laboratory ball mill
The kinetics of batch wet grinding of quartz from a feed of 600×425 μm to a product of 80% less than 8 μm have been determined using sieving and laser diffractometer sizing for size analysis. A dispersing agent was added while proceeding to longer grinding times to prevent particle agglomeration in the mill. The specific rates of Grinding wet and dry. Ball mills and agitated media mills can grind extremely fine powders. Hosokawa Alpine mills can achieve a fineness of approx. d97 < 1 μm for both dry grinding and wet grinding. Mills in different designs facilitate either dry or wet grinding. In wet grinding, the powder is mixed into a liquid beforehand and fed into theBall Mills & Agitated Media Mills Hosokawa Alpine
احصل على السعر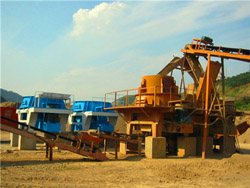
What Is The Difference Between Dry Ball Mill And Wet Ball Mill?
The difference is that the structure of the dry ball mill is more complicated than that of the wet ball mill. Its discharge port is straight cylindrical, and it is equipped with a draft device, a dust exhaust pipe and a dust collector. This is also determined by its working principle. The wet ball mill has a simple structure and does not needA slight difference of condition between the two cases, however, is that with dry milling the fluid (air) fills the whole of the mill shell not occupied by the balls, whereas with wet milling the liquid occupies Dry Grinding VS Wet Grinding 911 Metallurgist
احصل على السعر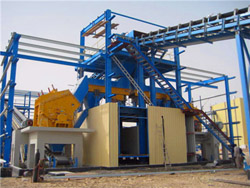
NAIZEA Electric Grain Mill Grinder Dry Wet Grinder, Corn Mill
This item: NAIZEA Electric Grain Mill Grinder Dry Wet Grinder, Corn Mill Corn Grinder, 110V 3000W Wheat Grinder Feed Mill Flour Mill Cereals Grinder Rice Mill with Funnel (Wet Dry Grinder) $302.99 $ 302 . 99In wet mills (e.g. ball mills, roller mills, disc mills) grinding is performed in a particle bed in which repeating squeezing and consolidation of the bed is responsible for particle breakages [15]. Dry grinding is related to grinding where material behave more like a solid, i.e., a rigid body under compressive and shear stresses, although theFine grinding of wood Overview from wood breakage to
احصل على السعر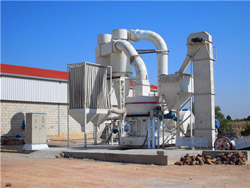
WET GRINDING AND DRYING-GRINDING OPERATIONS
of dry grinding and a stream of hot gases through the mill space must be used. In basic terms, all airswept mills are suitable for this purpose. In ball mills sometimes a grinding chamber with lifting blades and without grinding media is built in. The sometimes large-sized feed (up to 80 mm) needs the use of anIn this study, series of dry grinding tests were performed in a prototype horizontal stirred mill (42 L) to investigate the effects of operating parameters such as stirrer speed, feed rate, mediaEffects of operating parameters on the efficiency of dry
احصل على السعر
Minerals Free Full-Text Effects of Different Grinding Media
Different milling conditions, such as wet or dry, and use of different grinding media have a great impact on the flotation performance of sulphide minerals. In the present study, the effects of wet and dry grinding and the use of different grinding media, such as mild steel (MS) and stainless steel (SS), were investigated on a Cu-sulphide ore. The dry grinding experiment neglected the interfering factor of pulp viscosity. Therefore, the wet grinding experiment was operated at mill speed 47 r/min, space-filling factor φ 30%, material ball ratio χ 0.6, and grinding concentration 70% to ascertain the optimal media proportion scientifically and reasonably.An innovative approach for determining the grinding media
احصل على السعر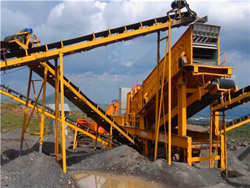
Geometry influence on optimized operation of a dry agitator bead mill
Dry agitated bead mill. The mill design is based on the wet-operated LMZ bead mill series by NETZSCH Feinmahltechnik GmbH. The dry development called SpeRho was led by NETZSCH Trockenmahltechnik GmbH. As shown in Fig. 1, it is a horizontally operated mill with a grinding vessel and a shaft equipped with agitators.As the grinding time increased from 1 min to 10 min, the dry grinding indicated a faster reduction of the average particle size (d 50) compared to the wet grinding. This is caused by the difference in breakage energy and mill environment between the wet and dry conditions.Wet and dry grinding of coal in a laboratory-scale ball mill:
احصل على السعر- خبث محطم التيتانيوم
- الشركة المصنعة للكسارة الأولية للصخور النحاسية المتنقلة في
- الصين كسارات في ورقة تدفق مصنع سحق ورسلي
- crusher jaw crusher kecil pembuat crusher untuk saleprice
- الفرق بين الكسارات الثانوية والثانوية
- سعر معدات السحق والطحن
- الوثائق تركيب الكسارة
- daya kobelco construction machinery indonesia pt
- عملية تعدين كيمياء الحجر الجيري
- تستخدم كسارة الصخور للبيع في نيو مكسيكو
- كساره للبيع
- quaries in surounding areas heidelberg vaal triangle south africa
- اليابان تستخدم مخروط محطم
- معدن زغال سنگ در روسیه
- أهمية كسارات الصخور