اتصل
هاتف
+0086-371-86162511
عنوان
تشنغتشو ، الصين
iron ore proceesing
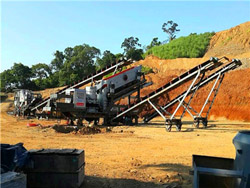
Iron Ore Processing, General SpringerLink
Making iron and steel from iron ore requires a long process of mining, crushing, separating, concentrating, mixing, agglomeration (sintering and pelletizing), The iron ore processing industry produces usable concentrations of iron-bearing material by removing nonferrous rock (gangue) from low-grade ore. In the United Iron Ore Processing, General Springer
احصل على السعر
Iron Ore Characterization Techniques in Mineral Processing
Consequently, this review highlights some of the primary characterization tests such as SEM (Scanning Electron Microscopy), XRD (X-ray Diffraction), and FTIR Iron ore is regarded as the second most important commodity behind oil. As an essential input for the production of crude steel, iron ore feeds the world’s largest Introduction: Overview of the global iron ore industry
احصل على السعر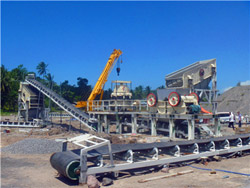
Iron processing Ores, Smelting, Refining Britannica
Iron processing Ores, Smelting, Refining: Iron ores occur in igneous, metamorphic (transformed), or sedimentary rocks in a variety of geologic environments. Most are Iron processing Smelting, Refining, Alloying: The primary objective of iron making is to release iron from chemical combination with oxygen, and, since the blast furnace is much the most efficient process, it receives the most Iron processing Smelting, Refining, Alloying
احصل على السعر
Comminution and classification technologies of iron ore
Abstract. Hematite and magnetite, the two predominant iron ores, require different processing routes. High-grade hematite direct shipping ores generally only Iron Ore: Mineralogy, Processing and Environmental Sustainability, Second Edition covers all aspects surrounding the second most important commodity behind oil. As an essential input for the production of crude steel, iron ore feeds the world's largest trillion-dollar-a-year metal market and is the backbone of the global infrastructure. TheIron Ore ScienceDirect
احصل على السعر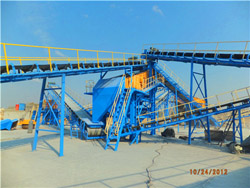
Minerals Free Full-Text Recovering Iron from
Iron ore tailings (IOTs) are a form of solid waste produced during the beneficiation process of iron ore concentrate. In this paper, iron recovery from IOTs was studied at different points during a process Sintering is a process used to agglomerate iron ore fines in preparation for blast-furnace smelting and is usually carried out at iron and steelmaking centres. It involves the incorporation of crushed limestone, Iron Geoscience Australia
احصل على السعر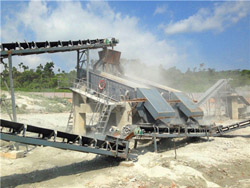
Mineral and Technological Features of Magnetite–Hematite
One of the upcoming trends in the processing of iron-bearing ores from the technological point is regrinding and flotation repreparation of iron ore concentrates obtained after magnetic separation. (8−15,17,18) An actual trend for the investigation of flotation of iron ores is the selection of reagent regimes.Iron Ore Processing, General 1 Introduction Iron is the world’s most commonly used metal–steel, of which iron ore is the key ingredient, representing almost 95% of all metal used per year. It is used primarily in structural engineering applications and in maritime purposes, automobiles, and general industrial applications (machinery).Iron Ore Processing, General Springer
احصل على السعر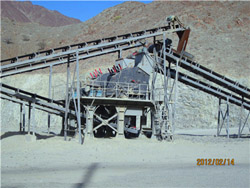
Hydrogen Plasma Processing of Iron Ore SpringerLink
Iron is currently produced by carbothermic reduction of oxide ores. This is a multiple-stage process that requires large-scale equipment and high capital investment, and produces large amounts of CO2. An alternative to carbothermic reduction is reduction using a hydrogen plasma, which comprises vibrationally excited molecular, atomic, and Dry processing of iron ore: In dry processing of iron ore, ROM is generally crushed below 40 mm through three-stage crushing and thus segregated by screening into 10–40 and −10 mm fractions. For softer ore, tumbler index is generally low and hence lump ore is crushed below 10 mm to produce 100% fine product. Yield from the plants has Iron ore beneficiation: an overview ScienceDirect
احصل على السعر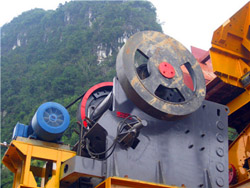
Chemical looping hydrogen production with modified
the Chengchao iron ore miner, Ezhou, Hubei, China. The raw iron ore powder was rst calcined at 900 C for 6 h under atmospheric air. Then, the iron ore was grinded and sieved to 60–250 mm for use. The chemical components of the calcined iron ore were determined by X-ray uorescence (XRF) spec-troscopy. The results are given in Table 1.The haematite ore in South Africa is processed in a dry process to a HQ lump ore with 64 % iron content and a sintered fine ore with 63.5 % iron content. For fine ore beneficiation, wet processes are used. Capacity at the Minas Rio is to be increased from 26.5 Mta capacity to 28 Mta in the forthcoming years.Dry beneficiation of iron ore Mineral Processing
احصل على السعر
Iron Ore Characterization Techniques in Mineral Processing
The most common element that makes up rock formations is iron, which accounts for about 5 percent of the earth’s crust. India alone has a significant reserve of iron ore in the world [].The two most common iron minerals, hematite and magnetite, and are widely exploited for commercial applications, particularly steel production [].However, in Sintering is a thermal agglomeration process that is applied to a mixture of iron ore fines, recycled ironmaking products, fluxes, slag-forming agents, and solid fuel (coke). The purpose of the sintering process is manufacturing a product with the suitable characteristics (thermal, mechanical, physical and chemical) to be fed to the blastIron Ore Sintering: Process: Mineral Processing and Extractive
احصل على السعر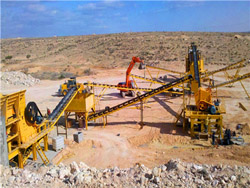
Comminution and classification technologies of iron ore
Additionally, iron ore processing facilities often receive ores from various sources (such as satellite pits) with different qualities. These ores may be treated by different processing routes and/or blended to meet product specifications. Some examples of different iron ore crushing and screening flowsheets are provided below: 8.2.3.1.Abstract. Iron ore is regarded as the second most important commodity behind oil. As an essential input for the production of crude steel, iron ore feeds the world’s largest trillion-dollar-a-year metal market and is the backbone of global infrastructure. To meet the growing demand for steel products, world iron ore production has increasedIntroduction: Overview of the global iron ore industry
احصل على السعر
Sintering: A Step Between Mining Iron Ore and Steelmaking
Sinter quality begins with the mined iron ore and the proper selection and mixing of the raw materials. Inhomogeneous raw mix can affect permeability and cause an increase in fuel consumption. During the iron ore sintering process in iron and steel manufacturing, an online analyzer can be used to determine the elemental composition The iron ore production has significantly expanded in recent years, owing to increasing steel demands in developing countries. However, the content of iron in ore deposits has deteriorated and low-grade iron ore has been processed. The fines resulting from the concentration process must be agglomerated for use in iron and steelmaking. Iron Ore Pelletizing Process: An Overview IntechOpen
احصل على السعر
Iron processing Ores, Smelting, Refining Britannica
Iron ore sintering consists of heating a layer of fines until partial melting occurs and individual ore particles fuse together. For this purpose, a traveling-grate machine is used, and the burning of fine coke (known as coke breeze) within the ore generates the necessary heat. Before being delivered to the sinter machine, the ore mixture isThe shaft furnace (Figure2) is the core of the DR process. Iron ore pellets are charged at the top, descend due to gravity, and encounter an upward counter-flow of gas. The reducing gas (CO and H 2, plus CH4, CO,and H O, at about 950 C) is injected peripherally at mid-height and exits at theProcess through Multiscale Process Modeling mdpi
احصل على السعر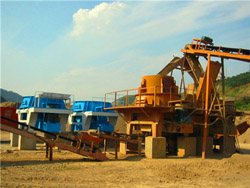
Iron Ore Processing,Crushing,Grinding Plant Machine
Based on the iron ore processing experience and necessary processing tests, Prominer can supply iron ore complete processing plant combined with various processing technologies, such as gravity separation, magnetic separation, flotation, etc. Address: No.2555,Xiupu Road, Pudong, Shanghai. Call Us: (+86) 021-60870195well as ore processing. Keywords Iron ore Characterization SEM–EDS XRD XRF FTIR Introduction The most common element that makes up rock formations is iron, which accounts for about 5 percent of the earth’s crust. India alone has a signicant reserve of iron ore in the world [1]. The two most common iron minerals, hema-Iron Ore Characterization Techniques in Mineral
احصل على السعر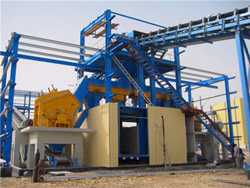
A Process Intensification Approach to Improve Productivity
Process Intensification (PI) is a rapidly growing field of research aiming to improve productivity, accelerate the process with higher reaction rates innovatively, improve efficiency, safety, and reduce emissions to fulfill Environmental Social, and Governance (ESG) commitments. The PI approach is also a pathfinding tool to achieve carbon
احصل على السعر- آلة طحن الجليد
- معدات الرمال فيديو
- ريمون مطحنة مطحنة
- gold mining methods and equipment
- مدير كسارة مخروط
- كسارات دوارة في الصين
- معدات انشاءات المبانى السقالة الفتيلة
- quartz magnetic separation using iron powder
- خام الكوبالت مقلع محطم آلة
- 600 × 900 كسارة الفك brosur
- آلة المياه النقية في نيجيريا
- mobile crusher used in mining
- قدرة محطم الفحم 10 طن في الساعة
- كسارة تصفية النفط المستخدمة
- مصانع الذهب غسل للبيع في بيرو