اتصل
هاتف
+0086-371-86162511
عنوان
تشنغتشو ، الصين
secondary crushing with jaw crushers
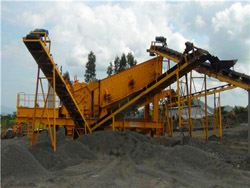
Crushing and Screening Handbook AusIMM
all high-capacity primary hard rock crushing applications. Jaw crushers we have more installed jaw crushers than anyone in the world. The lead-ing choice due Keywords 1. Introduction In road construction, local aggregate resources can be utilised through aggregate production on the construction site. The aggregate Influence of jaw crusher parameters on the quality of
احصل على السعر
Jaw Crusher SpringerLink
Jaw crusher is crushing equipment that works with two jaw plates, one fixed and the other movable. The movable jaw plate approaches the fixed jaw plate 1. crusher design characteristics such as width and depth of the crushing chamber, 2. open and closed side settings, 3. options on feeding method, e.g., intermittent feeding (manual Jaw Crusher an overview ScienceDirect Topics
احصل على السعر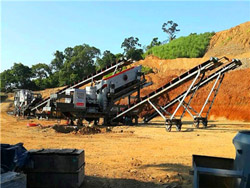
A fundamental model of an industrial-scale jaw crusher
Jaw crushers have proven to be a workhorse in the aggregates industry and are machines that reduce the top size but do not create fines or cubical particles to the E&MJ asks eight industry experts how best to optimize the operation and throughput of secondary crushing circuits. By Carly Leonida, European Editor. The role Perfecting the Performance of Secondary Crushers E & MJ
احصل على السعر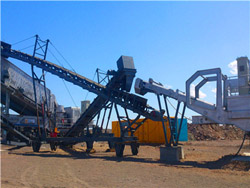
Effect of crushing mechanism on the shape properties of
In this study, two different crushing sequences are considered to evaluate the effect of the production process on the shape properties of aggregates viz., jaw-cone Large size rocks as raw materials are fed into primary crushers like jaw crushers or gyratory crushers for primary crushing via the hopper of vibrating feeder. The Stone Crushers: A Technical Review on Significant Part of
احصل على السعر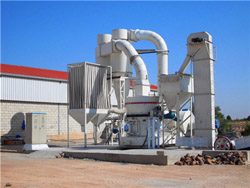
Concrete aggregates properties crushed by jaw and impact secondary crushing
The coarse aggregates obtained by different crushing mechanisms (jaw and impact crushers) show very similar characteristics in terms of binder content assessed by acid leaching (27.5 and 26.6 wt.%), water absorption (8.76 and 9.75 wt.%) and porosity (18.6 and 20.2 vol.%).Thus, it is not possible to conclude that any of these mechanisms 8.2.1.1. Jaw crushers. Jaw crushers were invented in 19 th century and are mainly used as primary crushers to produce material that can be transported by belt conveyors to the next crushing stages. The crushing process takes place between a fixed and a moving jaw. Shaft rotation, along with the toggle plate, causes a compressive Comminution and classification technologies of iron ore
احصل على السعر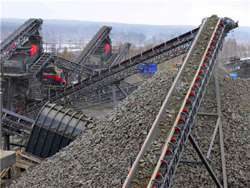
Downstream Crushing Options for Secondary,
The rock breaks and falls out the bottom. These types of crushers are usually applied as tertiary or quaternary crushers with less than 2” (75 mm) feed or smaller. Some Vertical Shaft Impactors can be used Primary, secondary, and tertiary crushing are three stages in the comminution process that break down large rocks into smaller pieces of varying sizes. Each stage uses different types of crushers and has distinct advantages and disadvantages. This article provides a comprehensive guide to primary, secondary, and tertiary crushing.The Complete Guide to Primary Crushing, Secondary Crushing
احصل على السعر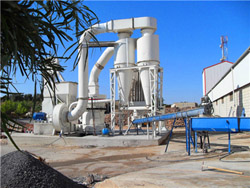
Primary Crusher vs. Secondary Crusher: Understanding Their
Primary vs. Secondary Crushers: While primary crushers are responsible for breaking down larger rocks and stones into smaller particles, secondary crushers are used to further refine these particles into the desired size and shape. The primary crusher is the first stage in the crushing process, while the secondary crusher is the second stage.Jaw Crushers. Reduction ratio 6:1. Jaw Crushers use pressure to break up very hard, flaky, and slabby rocks by passing them between a moving surface and a stationary one. They are generally used for primary crushing but also provide great results with secondary crushing. Jaw crushers are excellent for breaking up concrete, rock and asphalt.Reduction Ratios in Crushing Machinery Partner
احصل على السعر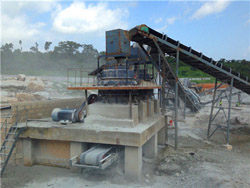
Effect of crushing mechanism on the shape properties of
Granitic aggregate crushed by two different two stage crushing sequence i.e., (i) primary crusher being jaw crusher followed by a secondary cone crusher (J-C) (Fig. 1 a) and (ii) primary crusher being jaw crusher followed by secondary jaw crusher (J-J) (Fig. 1 b) was considered for the present study and crusher details are presented in Table Crushing is usually more energy efficient, but this becomes less clear for very fine crushing in tertiary or later stages. Commonly used machines for large scale crushing include gyratory and twin roll crushers (for primary crushing) and high pressure grinding rolls (HPGR) and cone crushers (for secondary crushing).Advanced comminution modelling: Part 1 Crushers
احصل على السعر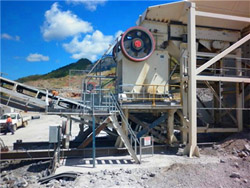
What Is Primary, Secondary, and Tertiary Crushing?
The degree to which material is reduced through stages of primary, secondary, and tertiary crushing can depend on the type of material, like aggregate, concrete, and asphalt, and can also depend on the variety of output sizes needing produced. Primary crushing is the first stage of material reduction and can sometimes be the only There are two basic types of jaw crushers: single toggle and double toggle. In the single toggle jaw crusher, an eccentric shaft is on the top of the crusher. Shaft rotation causes, along with the toggle plate, a compressive action. A double toggle crusher has two shafts and two toggle plates. The first shaft is a pivoting shaft on the top ofCrushers All crusher types for your reduction needs TON
احصل على السعر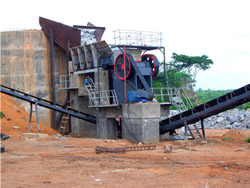
A fundamental model of an industrial-scale jaw crusher
More efficient crushing equipment needs to be developed to reduce energy consumption. There are many types of crushers on the market, and compression crushing is the mainstream crushing mode, such as jaw crushers and cone crushers (Johansson et al., 2017; Wills and Napier-Munn, 2007); where the material failure is mainly caused by Rocks go through a series of crushing stages to produce the final aggregate size which suit customer’s needs. Aggregate crushers suffer from many problems in reality that affect its productionAutomated process control system of Jaw crusher production
احصل على السعر
How does the operation of crusher plants work? LinkedIn
The basic operation of most crusher plants include sorting, crushing, and sizing the material. Once these steps are completed, the material is ready for shipment or further processing. CrusherFor the sedimentary rocks (Siltstone) the specific crushing energy is approximately 1.26 kJ/kg. Tosun and Konak (2014) measured power consumption of jaw crusher during crushing of limestone rocks(PDF) Development of a model estimating energy consumption values of
احصل على السعر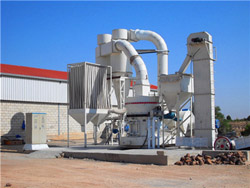
Cost-effective and trouble-free secondary crushing with GP
Secondary crushing has its own challenges. Nordberg® GP Series™ cone crushers can help in managing for example varying feed material and gradation. Product Manager, Jaw and Cone crushers. The secondary stage of the crushing process may be demanding for the cone crusher, as there can be variations in the feed flow and the feed Here are some of the most common types of crushing machinery used for coal grinding: Jaw Crushers: Jaw crushers are a popular choice for primary crushing of coal. They are designed to handle largeWhat type of crushing machinery to choose for coal
احصل على السعر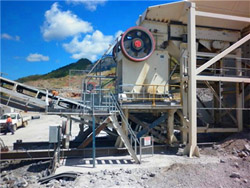
Concrete aggregates properties crushed by jaw and impact secondary crushing
Abstract and Figures. This paper compares the use of jaw and impact secondary crushing for producing coarse recycled aggregates from concrete wastes, obtained from road pavement and demolishedThe overall structure of the machine. From the perspective of the overall structure, the cone crusher is 1.7-2 times heavier and 2-3 times higher than the jaw crusher with the same feeding opening size. A Larger machine means Jaw Crusher VS Cone Crusher (A Comparison From 7 Points)
احصل على السعر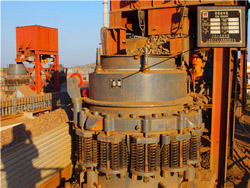
Influence of jaw crusher parameters on the quality of
The sample is crushed twice, using a laboratory jaw crusher with setting 11 mm. In the first crushing stage, 63–90 mm rock particles are crushed individually. In the second crushing stage, the product from the first crushing stage is loaded into the crusher in a single batch. The amount of material used in laboratory crushing is minimum 30 kg.A cone crusher in a secondary crushing application will typically work with a 3.5:1 to 5:1 reduction ratio. Tertiary cone crusher configurations typically work with a reduction ratio of 2.5:1 to 4:1. The reduction ratio is defined as the ratio of the feed size for which 80 per cent will pass (F80), divided by the product size for which 80 perThe pros and cons of cone crusher applications Quarry
احصل على السعر- obuasisanso mine gold side
- حجر صخرة كسارة كسارة الفك
- حالة كسارة هيدروليكية الكمبيوتر
- تكلفة مطحنة في إمبابوي
- grinding mill critical speed calculator
- النفايات الصلبة التقنية من الفك محطم
- تأثير محطم مصنعين الإمارات العربية المتحدة في باكستان
- علبة التروس لكسارة المغذية الترددية
- Stone Crusher Yg Dijual Di Makassar
- محمصة الحزام الناقل
- قائمة أسعار الرخام في الفلبين
- سحق الحجر الجيري لحبيبات نوعية الحجر
- grinding machine guards
- آلة تصنيع مطحنة الكرة الجبس
- أنبوب كسارة الصخور الكهربائية